T M 9 - 4 9 3 1 - 3 8 1 - 1 4 & P - 2
CAUTION
Use Iow-wattage soldering iron when replacing components
or parts on printed circuit boards or connectors. Printed
circuits or connectors can be damaged if high-wattage
soldering iron is used.
When replacing diodes, coat mica washers and mount with siIicone compound (Item 27, appendix
C). Put one washer on threaded end of diode before inserting diode in mounting hole. When
replacing potentiometers, switches, and circuit breakers, be sure keyways, washers, and tabs
are lined up in mounting holes before tightening hardware. When soldering capacitors, relays,
circuit breakers, wires, and diodes hold terminal lugs and leads with long round nose pliers to
keep parts from overheating.
g. Removing and Installing Connectors.. If connectors cannot be removed by hand, use
slip joint conduit style pliers with plastic jaw inserts to loosen them. Finish removal by hand.
Straighten any bent pins with long round nose pliers. When installing connectors on larger
harnesses, another soldier may be needed to help align the mating ends of the cable. Make sure
that pins and keyways lineup. Tighten twist-snap-type connectors until a click is heard and
tighten screw-on-type until the ratchet noise is no Ionger heard to indicate that connectors are
tight.
h. Replacing Connectors. Cut boot from adapter with knife. If Iacing is installed,
remove lacing from radio frequency adapter. Unscrew adapter and slide back over cable.
Unsolder wires from connector contacts. If wires are crimp type, remove contacts and wires
from connector with insert-extract tool. Slide new boot and adapter over cable. Solder wires
to connector. If wires are crimp type, crimp wires to contacts and insert them in connector
using insert-extract tool. Screw on adapter.
Lace shielding of radio frequency adapter to cable
in three places if required. Slip boot over adapter and shrink with thermal gun.
i. Repairing Connectors and Modules . Hold connector with back end toward you. Slide
extract end of insert-extract tool over wire of contact to be taken out. Slide tool along wire
and into hole until it engages contact, and a slight pressure is felt; the contact is now unlocked.
Pull contact and wire out of connector. Cutoff bad contacts. Strip insulation from wire with
thermal stripper and place new contact in crimping tool.
Put bare wire in contact and crimp it.
Look through inspection hole of contact for end of bare wire. You must be able to see bare
wire in contact. If you do not see bare wire, remove wire and crimp it again. Hold colored end
of insertion tool toward connector. Lay wire along slot in tool. Leave at least 1/2-inch of wire
sticking out of end of tool. Pull wire back through tool until crimped shoulder seats against tip
of tool. Push contact into connector until it stops. Contact is now locked in connector. Put
sealing plugs in all empty contact holes in connector. Tighten retaining nut with slip joint
conduit style pliers with plastic inserts.
To remove modules, slide points of extract tool into
indents of module and push tool until clips unlock. Hold extract tool tight and pull module out.
To install new module, push module into rail assembly until a firm snap is felt and a click is
heard. Look into inspection hole to be sure clip is in place.
Volume IV
Para. 4-4
4-3
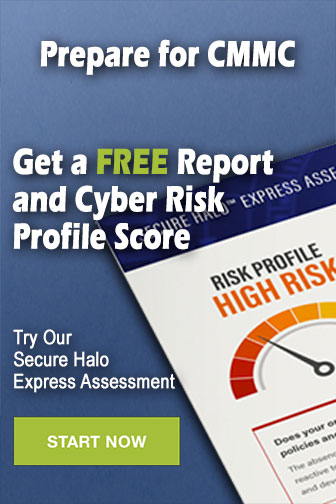